We work on quality from various aspects…
Our commitment to quality is a defined, detailed and delivered promise which is kept for every tablet, capsule and dry powder sachet of every batch.
We work on quality from various aspects that are put down with elaborate purpose and in practical steps. A strict adherence to these guidelines has helped us achieve consistency in formulating.
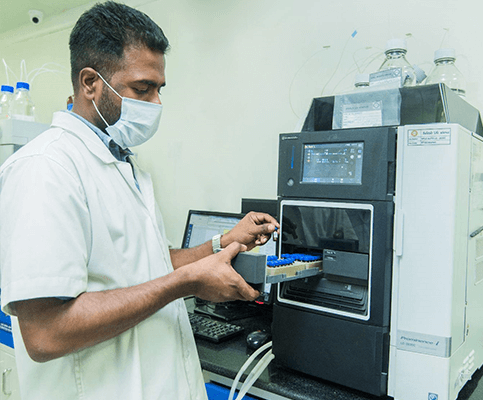

Standard Testing Procedures
Analytical and Verified Steps to Test Products at Every Stage. The management proactively sponsors all the QMS initiatives like personnel training and the implementation part is taken care of by the Quality Assurance (QA) department.

Quality Management Procedures
Sets Quality Pre-requisites at the Organisational Level

Standard Operating Procedures
For Consistent and Predictable Quality of Products and the Processes
Quality Management System
Quality Management Procedures, Standard Operating Procedures and Standard Testing Procedures form the concrete framework of our Quality Management System (QMS). Through these guidelines, and through standardised practices, we manifest the Quality Policy. A rational and inclusive arrangement of each step makes the process smooth and ensures a consistent and controlled output.
The management proactively sponsors all the QMS initiatives like personnel training and the implementation part is taken care of by the Quality Assurance (QA) department.
Quality Assurance
The QA department designs and maintains QMS for the company. It identifies the general and specific issues of the organisation and is involved in continuous improvement through preventive and corrective actions. While conducting stringent audits periodically, it enables the comprehensive, adequate and effective implementation of the QMS. Responsibilities of the QA department include:
QMS
Creating & Maintaining QMS.
Training
Training Personnel on QMS – New Employee Orientation and Periodic Reinforcement Trainings.
Adherence
Ensuring Adherence to QMS by all the Departments
Reporting any Non-conformance
Corrective Actions – Recommending Solutions to Quality Issues and Following Up Issues to Resolution Preventive Actions – Proactive Action to Prevent the Occurrence of Quality Issues
Controlling Non-Conforming Products
Controlling Non-Conforming Products Until Corrective Action
Feedbacks
Providing Periodic Feedbacks to Management on Quality Status
Managing Complaint
Managing Complaints & Recalls
Quality Control
From raw material induction to in-process testing to finished product testing, the Quality Control department plays an important role at every stage of the product life cycle. The identity, purity, stability and potency of the products is established and ensured through rigorous adherence to predetermined specifications of globally approved Pharmacopeia (USP, BP and IP). Responsibilities of the QC department include:

Conducting physical, chemical and microbial tests on materials and products

Issue Certificate of Analysis (CoA)

Maintain equipment and resources in validated/qualified status